An article on peristaltic hose pumps and the insights in traditional markets. Also discover why they are suitable for heavy duty applications.
A peristaltic pump is, by design, one of the most flexible types of pumps available. Because it can pump liquids with a huge variety of different physical characteristics, it is the ideal pump choice for many applications in many different industries. Another significant advantage that peristaltic pumps have over other types of pumps is that the process fluid is completely contained within the pump’s hose. This translates into easier and more cost effective maintenance of the pump – there are no mechanical seals or glands to replace and the lack of any type of seal means that the pump is safer to use. Corrosive or chemically active fluids are completely contained within the hose. The combination of being able to pump fluids of varying density, viscosity, reactivity, and abrasiveness, or with variable solid content, along with its complete containment, make this type of pump extremely versatile.
This type of pump stands out in applications where others face serious challenges. Hoses of different material and size allow this pump to perform at its best no matter the application. Although it’s well known in the slurry and sludge removal community, it’s peristaltic action is perfect for use in applications where shear sensitive material, requiring a gentle pumping action, is pumped. Examples include flocculants, shear sensitive polymers and delicate cell cultures.
Peristaltic pumps have become more widely known outside their traditional industrial sectors, thanks largely to the advantages discussed above. Their ability to fully contain the process fluid not only makes them ideal from a safety point of view, but, because the product is completely isolated and contained within the pump’s hose, there is no possibility of contamination, a critically important feature in the food and beverage as well as the pharmaceutical sectors. Another industry starting to take notice of peristaltic hose pumps is the printing and packaging sector. Previously, air-operated diaphragm pumps were used to pump viscous, polymer-containing, shear sensitive inks. Thanks to its advantageous features, the peristaltic pump is now routinely used in place of the air-operated diaphragm pumps.
Often overlooked is the total cost of pump ownership. The peristaltic pump’s lack of any mechanical seals or glands makes it very inexpensive to maintain. The only replacement part on the pump is the hose. Today’s peristaltic pumps have low cost replacement hoses that are easy to change. Although these may seem like small considerations, the cost savings that these features translate into through decreased downtime and lower maintenance costs can positively impact the bottom line in our current austere economic climate.
Hose improvement leads to wider pump deployment
Significant improvements in hose design and manufacturing have improved their service life dramatically. New hose materials now include those resistant to many classes of aggressive chemicals; organic solvents, oils and fuels, and they provide performance under a variety of temperatures and environmental conditions. Food grade materials are also available so that peristaltic pumps can be utilised where hygiene is a concern, for example in the food and beverage or pharmaceutical industries. In addition to the improvements in hose materials, the manufacturing process has also been improved. Because of the way peristaltic pumps work, the hose is the part that wears. Historically, hoses could suffer from accelerated wear, due in part to the way they were manufactured. To ensure a uniform wall thickness, the outside walls of the hoses were subjected to secondary machining. Extra stress during hose manufacturing led, in some cases, to early hose fatigue, failure and a disappointing service life. New manufacturing processes that ensure uniform wall thickness without secondary machining has improved the service life of hoses considerably.
Traditional peristaltic pump markets
Extensively used in the mining industry, where process fluids with a high percent of solids and/or high specific gravity mean that other pump technologies fail, peristaltic pumps are able to cope with the rough environments and extreme pumping tasks that characterise the mining industry. Diaphragm pumps lose efficiency, due to the corrosive nature of the reagents, increasing cost due to excess chemical usage. Positive displacement pumps, such as progressive cavity pumps suffer from failed rotors and stators because they are allowed to run dry. It is these grueling conditions, coupled with the peristaltic pump’s advantages, which led to the widespread uptake of peristaltic pumps in the mining industry.
New market sectors for peristaltic pumps
The same advantages that led to the peristaltic pump’s success in the mining industry have led to new opportunities in industries not traditionally associated with peristaltic pump use. The pulp and paper industry is one area where peristaltic pumps have made gains. A peristaltic pump can run dry and can pump at very low pump rates. The pulp and paper industry processes wastewater that contains a large amount of fibrous material, chemicals and filler. This tends to clog pumps when pumped at a low flow rate. Because of this, the efficiency of other pump types is compromised. Typically the clog happens on the suction side. The peristaltic pump’s ability to reverse it’s flow direction –just by reversing the rotation direction of the rotor– allows the peristaltic pump to easily overcome this challenge.
Ink management in the packaging business is another sector that is seeing a growth in peristaltic pump use. AODD pumps are traditionally used to move inks from storage to printing machines. Production problems result from the fact that AODD pumps can introduce air into the ink while pumping. This leads to bubble formation within the ink, ruined packaging and both an increase in costs and an increase in waste disposal. Ink dispensed using a peristaltic pump is the ideal solution to this problem. The ink is dosed gently, preventing any bubble formation. Additionally, as the ink is enclosed within the hose, this reduces mess, cleanup time and allows for quick change of ink colour, by changing the hose. Yet another industry where peristaltic pumps are gaining in market share is the brewing and baking industries. Both of these sectors need to transfer fluids containing yeast. Yeast transfer presents several challenges to a pump. Yeast are shear sensitive, so they must be pumped as gently as possible. During their growth, the viscosity of the fluid changes from around 1 centipoise, the viscosity of water, to several thousand centipoise. Finally, yeast produce gaseous CO2 when they are healthy, leading to possible vapour lock with some pump types. Although yeast are biological reagents, they are also notoriously abrasive, causing stator or impeller wear, leading to increased maintenance and replacement costs. All of these challenges are solved using a peristaltic pump. Peristaltic pumps can handle viscous, abrasive fluids in a gentle manner with low shear and are not susceptible to vapour lock.
Peristaltic pumps are also becoming popular to accurately dose drugs in clinics. Human error can result in incorrect drug dosage and an automatic dosing method can reduce errors, increasing patient safety. In some methadone clinics in the UK, peristaltic pumps are being used to treat recovering addicts. The peristaltic pump’s design ensures accurate dosing and the high degree of repeatability required by government legislation. At the same time, hygiene is maintained, as the dispensed drug, methadone is completely contained within the pump’s hose, which was specified to be resistant to the known acidity of the drug. Adding these benefits for patients while still maintaining simplicity of use by staff makes these pump’s attractive. No specialised training or tools are required to change the tube and once the tubing is used, it can be safely disposed.
Finally, in an unusual example of how peristaltic pumps can be effectively deployed for challenging tasks, a manufacturer required a pump to be installed in a vending machine that dispensed hot chocolate. The pump was to be used to transfer chocolate syrup to the cup. The challenge was that the installation was in sub-zero temperatures, where the syrup becomes highly viscous. In order to deliver an accurate dose, under hygienic conditions, at a constant flow-rate, a peristaltic pump was chosen with specialised silicone food grade tubing that is rated for high temperatures. The peristaltic pump was further modified to provide excess suction for the highly viscous syrup.
Summary
The features of peristaltic pumps make them ideal for extreme pumping conditions in heavy-duty industries. But their advantages also extend their usefulness to other non-traditional market sectors. Having no mechanical seals, low maintenance, gentle pumping action, high suction capability, corrosion and abrasion resistance, reversibility, and ability to run dry gives these pumps the edge for a huge and varied number of pumping challenges in many different areas.
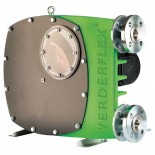